Journal #17
From the sublime, to the sustainable
Born out of a country that places sustainability at the forefront of its agenda, J Craft demonstrates how its environmental production practices are delivering for the company, the owners and the planet
Words by: Julia Zaltzman
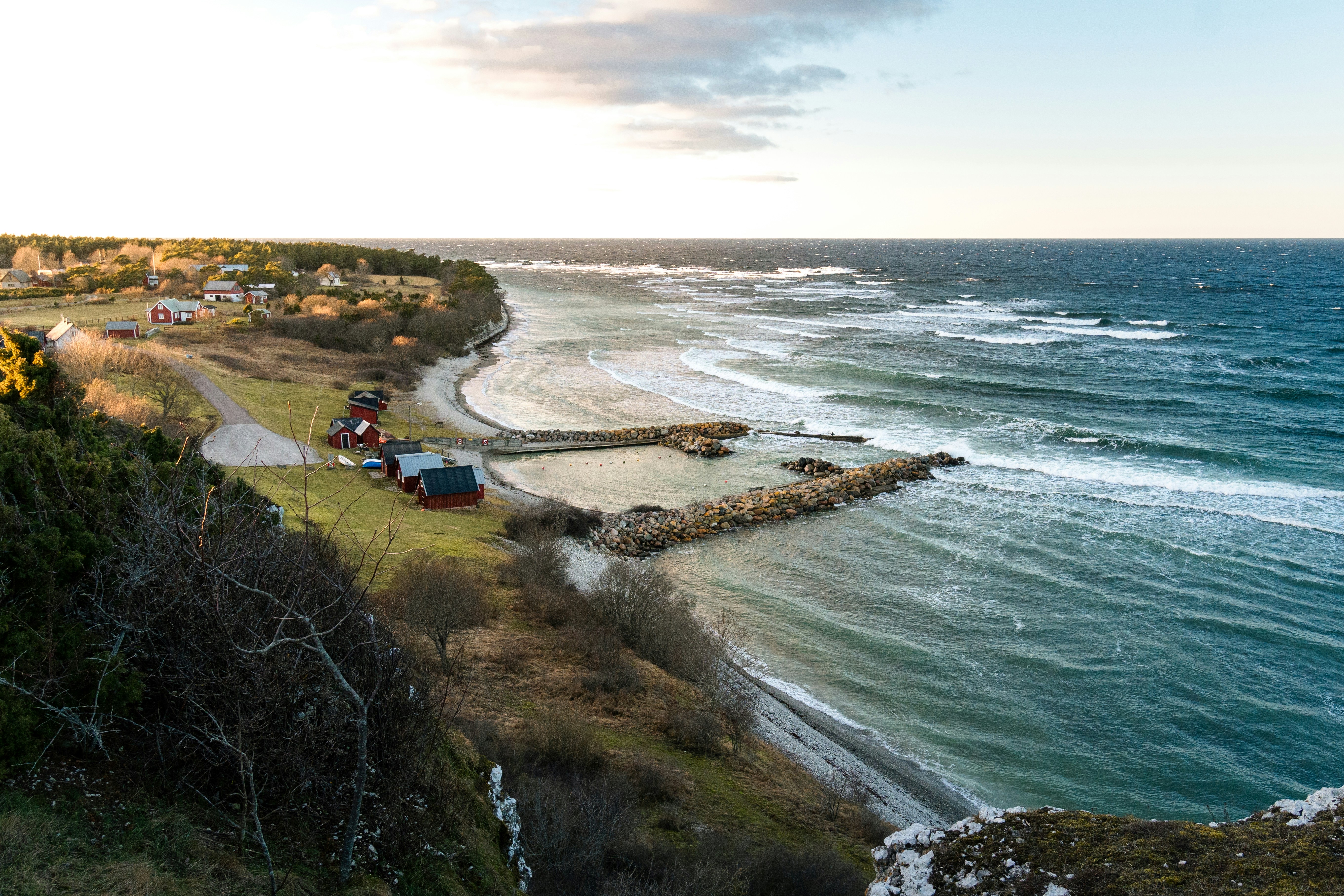
Scandinavia is the undisputed champion of sustainability. The Nordic countries, including Denmark, Finland, Iceland, Norway and Sweden, are at the forefront of the global green transition, leading the charge in a reduction of CO2 emissions and production of renewable energies. Sweden’s environmental laws are designed not only to regulate industries but encourage a societal shift towards sustainable practices. It’s not a fluffy, feel-good sentiment but a nationwide endeavour to improve and deliver, exemplified by it becoming the first country to produce fossil-free steel in 2021.
Copenhagen’s aim to be the first carbon-neutral capital by 2025 is driven by plans to implement a heating supply based primarily on biomass, waste and geothermal energy. It’s not surprising that a country responsible for giving the world “hygge” and clean-lined design should foster a sense of accountability for the environment. In turn, operating within some of the toughest global standards shapes brands like J Craft, which wraps a smorgasbord of skill, style and maritime heritage around its holistic approach to environmental protection.
Located on Sweden’s largest island of Gotland, J Craft’s boatbuilding pedigree runs as deep as the ancient Viking graves that lie beneath the capital Visby’s cobblestone streets. Embedded within its measured production practices is an unwavering commitment to responsibly sourced materials and an artisanal focus on quality over quantity. Company owner Radenko Milakovic’s outlook that ‘J Crafts are built for the few, not the many’ epitomises its sustainable, small-batch production methods.
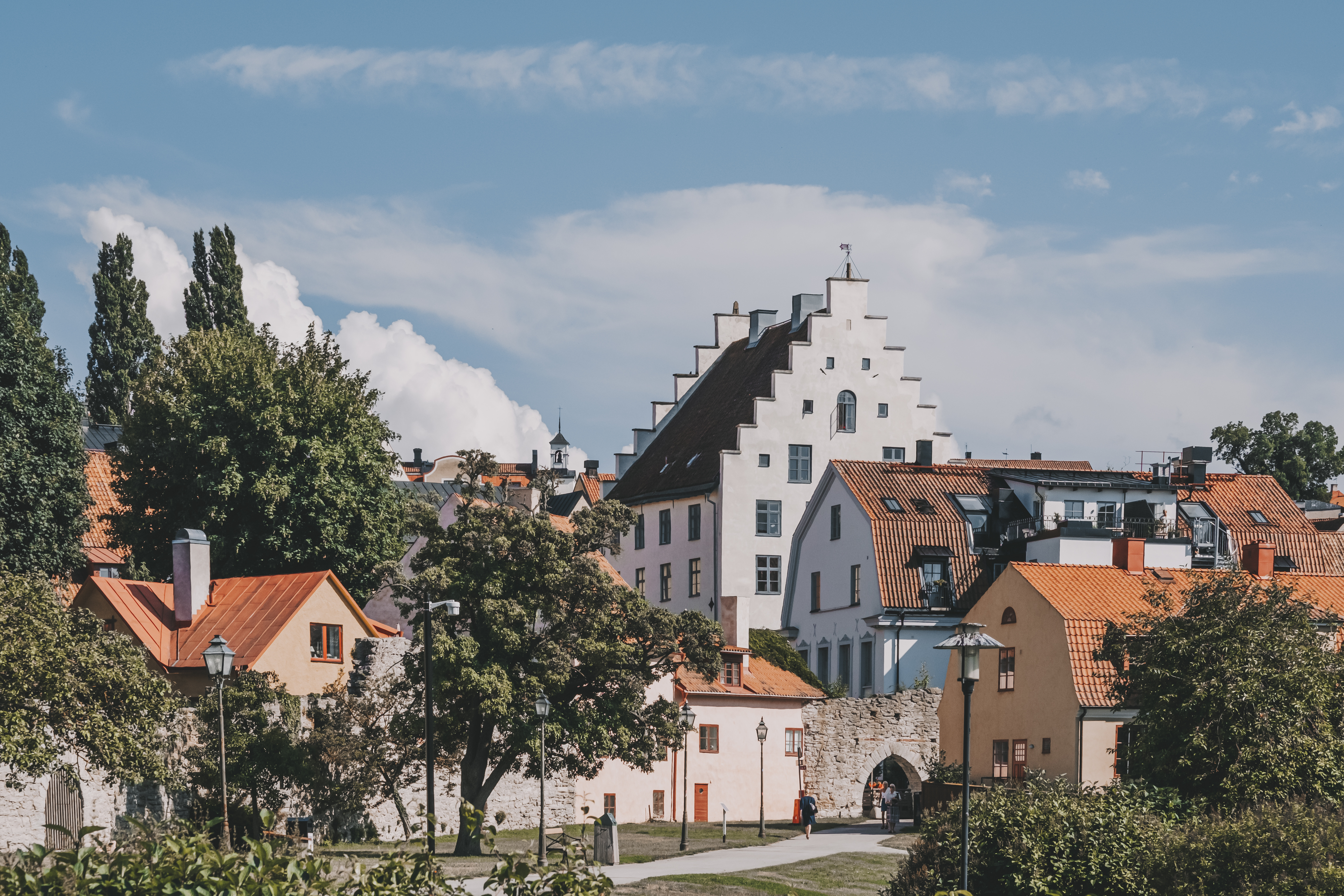
Handcrafted to order from the keel up, each boat takes between 8,000 to 10,000 work hours to complete. The paradox of mounting handcrafted mahogany veneer on a fibreglass hull that’s built to slice through the Baltic Sea is the essence of J Craft’s enduring appeal. It’s also a significant factor of its environmental philosophy, exemplified by the more than 1,000-year-old Viking technique used for curving solid wood parts. Steamed for a week at 120ºC until supple, the wood is quickly placed in a mould, bent by hand using clamps and left for a week to cool down. ‘You only get one shot as the wood becomes chemically and physically altered, so it’s a case of do it once and do it right,’ explains Johan Hallén, J Craft’s CTO and longest serving employee of 25 years.
The former navy mine diver-turned-carpenter built the first J Craft with the company founder, Björn Janson, and has overseen every build since. Like many of his Gotland-born colleagues, he first worked at leisure boat company Nimbus, which had a factory in Visby until 2008. In contrast to Nimbus’ serial production, J Craft’s bespoke methods are a source of enduring pride for the team, all of whom delight in marrying old-world craftsmanship with modern boatbuilding techniques.
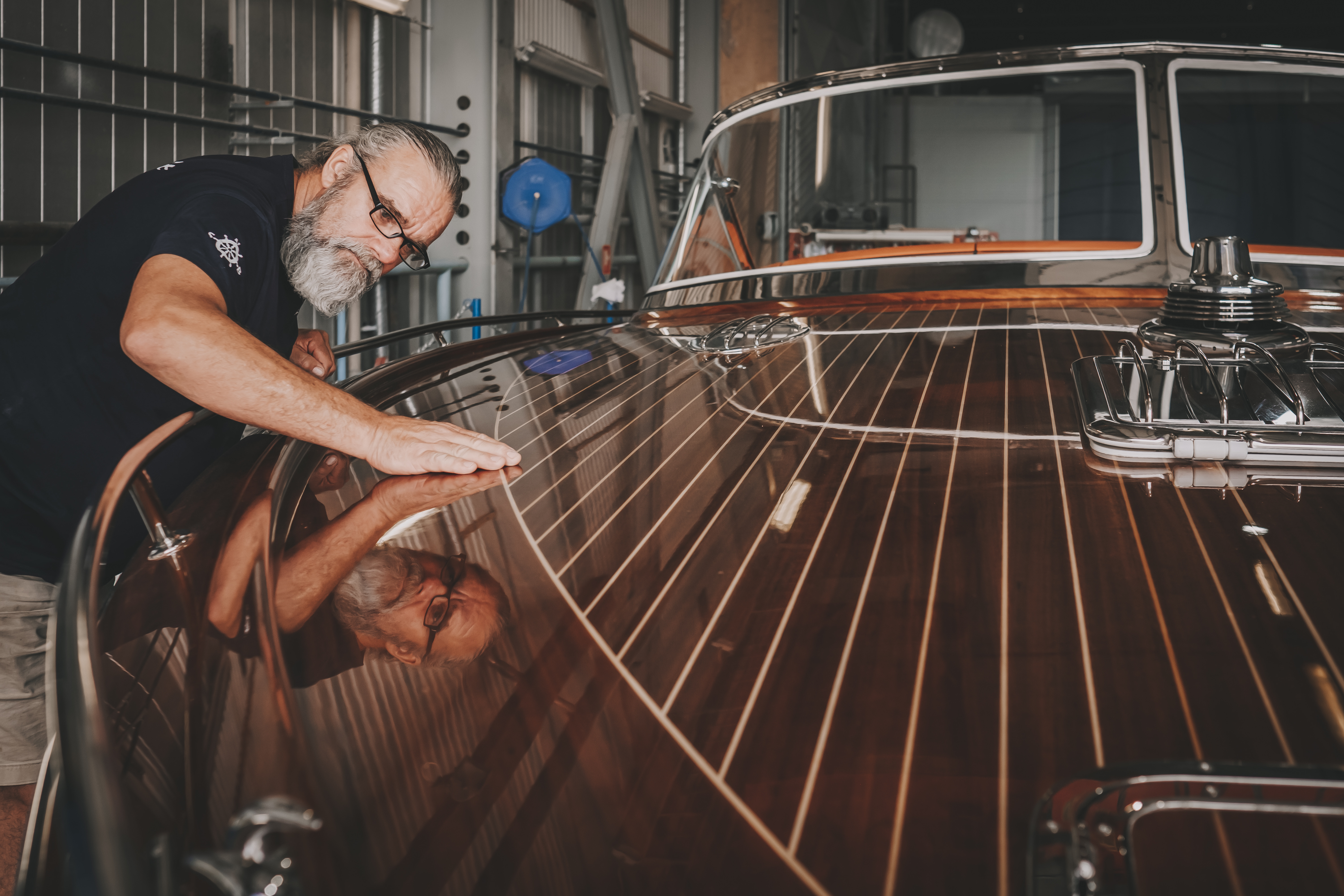
Case in point is J Craft’s core configuration department, which pumps recyclable vinylester resin between raw sheets to create a solid, lightweight and super-strong construction material. The technique of vacuum infusion, adopted by J Craft three years ago, is a revolution for the GRP (Glass Reinforced Plastic) department. In contrast to the wet and sticky hand-rolled technique used in boatbuilding since the early ’60s, injection resin is a dry closed process. It requires fewer solvents and delivers a superior result. Furthermore, when a J Craft reaches the end of its life, all the core materials are fully recyclable.
In 2008, when Radenko Milakovic bought the brand, he shelved the original Cabrio Cruiser model and started developing the evolved 42-foot Torpedo which was launched in 2009. In doing so, the J Craft team swapped out the old twin Yanmar engines for the latest generation of twin Volvo Penta IPS engines steered with a rudderless IPS pod system. This allows for a 20 per cent higher top speed (close to 50 knots) with 30 per cent less fuel consumption. The team spent a year with Volvo Penta’s naval architects developing the hull to perfect seakeeping – and therefore fuel – efficiency. A hybrid electric drive is anticipated to go into development next.
Further change came in 2021 when J Craft moved from its military shipyard in the far north of Gotland, neighbouring the smaller island of Fårö. Located north of Gotland, Fårö’s battered fishing huts stand sentinel by the water’s edge, where twisted trees crawl along the ground, beaten horizontal by ferocious winds. J Craft’s move to Visby brought a better supply chain and the chance to build a workshop from scratch with a reduced CO2 footprint. The entire plant is heated with wood chips, allowing for heat recovery to be used in all ventilation, from the GRP department to the air-demanding paint box. Plans are also afoot to install a large solar cell plant on the shipyard roof, to make the production site self-sufficient and fossil free in terms of its energy use. Then there’s the largely on-site production of most of the Torpedo’s component parts. An estimated 90 per cent-plus of every Torpedo by value-add is Swedish-made and sourced. By keeping parts and labour in- or near-house, J Craft maintains its exemplary quality control while minimising its carbon footprint. Parts that are not made by J Craft itself are preferably sourced from companies that use green energy in their production process.
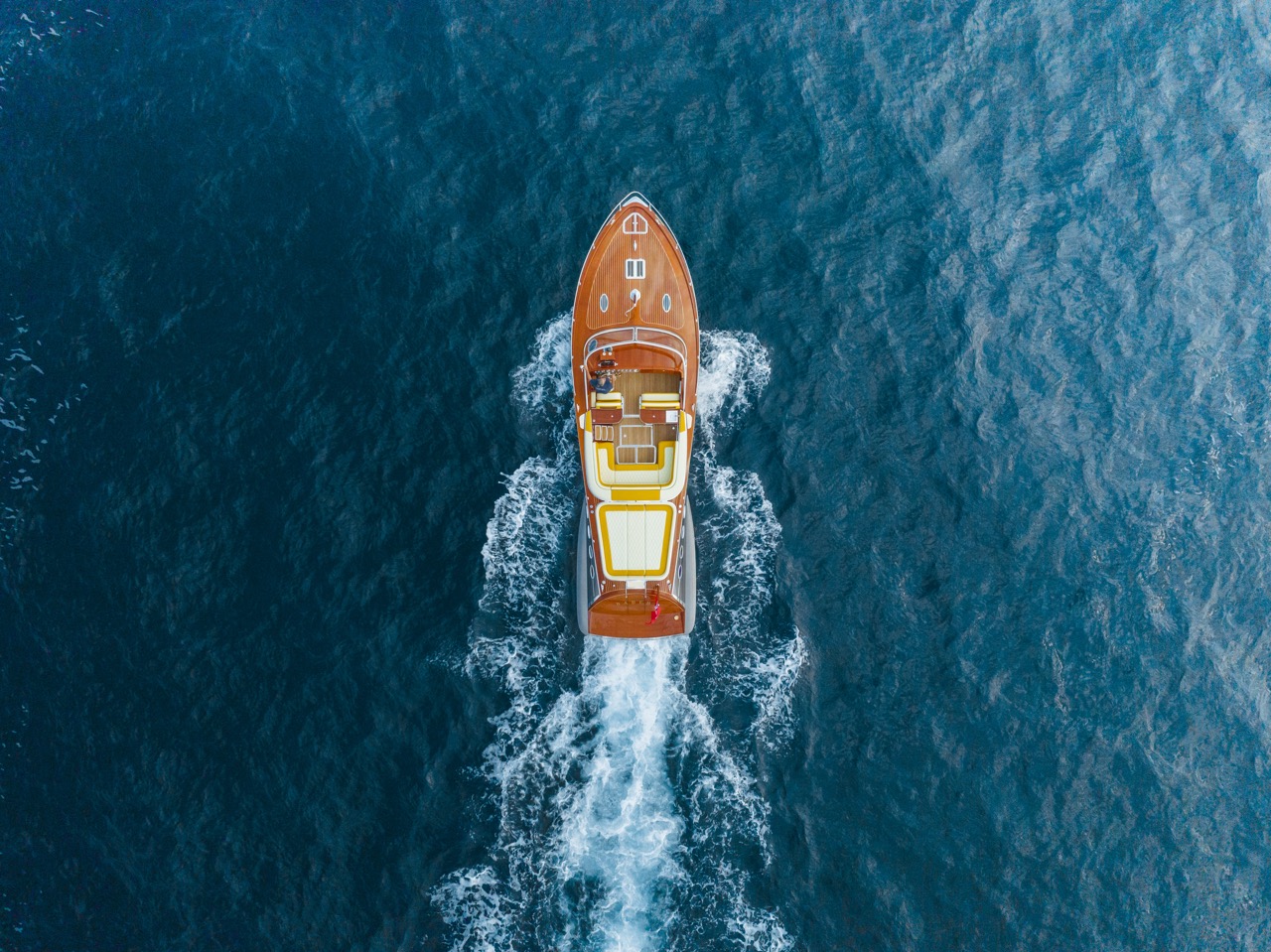
It's one thing to be a Swedish business, created and sourced in Sweden. It’s another to be a cohesive workforce where personal pride, brand ambition and national heritage go hand in hand with innovative production processes and sustainable business practices.
Julia Zaltzman is a journalist specialising in superyachts, travel and luxury lifestyle. She has written for The Times, The Telegraph, Robb Report and Boat International